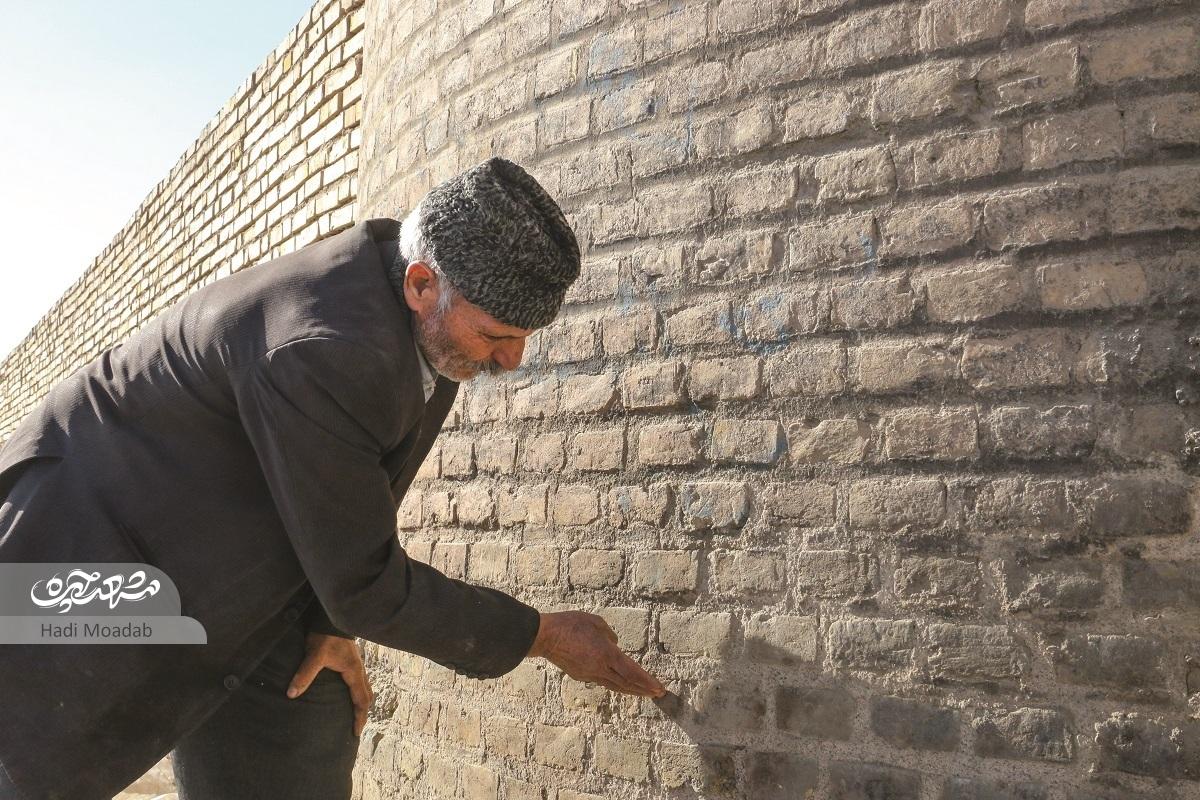
از اواسط دهه۳۰ به بعد با احداث زیرساختهای مهمی همچون فرودگاه، راهآهن، آرامگاه نادر و فردوسی، بوستان کوهسنگی، بازار رضا و البته توسعه برخی بناهای مهم دیگر بهویژه بارگاه منور امام هشتم (ع) و دانشگاه فردوسی و دهها سازه مهم دیگر، مشهد در مسیر نوسازی و توسعه قرار گرفت.
در این توسعه، یک واحد صنعتی و همت کارکنان آن نقش پررنگی داشت؛ کارخانهای که شکلگیری آن به سفر زیارتی رئیس اسبق اداره معادن کشور به مشهد برمیگردد. مرحوم مهندس علی زاهدی که پساز اتمام تحصیل در دانشگاه پاریس در سال ۱۳۰۹ به کشور بازگشت و کمی بعد به ریاست اداره معادن برگزیده شد. سال۱۳۳۲ را در جوار بارگاه منور امام هشتم (ع) آغاز کرد.
هنگامیکه او از حرم مطهر به محل اقامتش بازمیگشت، ماجرایی برایش اتفاق افتاد که در ادامه منجر به احداث یکی از کارخانههای عظیم شرق کشور شد. فرارسیدن روز صنعت و معدن بهانهای شد تا پای صحبت چند معدنچی بنشینیم که روایتهای مفصلی از احداث کارخانه سیمان شرق دارند.
غلبه بر کوهها، شکست سنگها و انتقال مواد اولیه به کارخانهای وسیع و تماشایی که در محدودهای خارج از حریم شهری قرار دارد و علاوه بر تأمین مصالح ساختمانی شهر و ایران، کشورهای مختلف دنیا طالب و خریدار سیمان آن هستند، همه در این روایت قرار دارد.
مرحوم مهندس علی زاهدی که سال۱۳۳۲ برای زیارت به مشهد آمده بود، در این شهر با مرد میانسال ارابهرانی از اهالی روستاهای شمال شهر مشهد روبهرو شد. در ارابه این مرد یک تکه سنگ بزرگ حمل میشد که در چشمان زاهدی، آن مرد و سنگش شبیه علاءالدین و غول چراغ جادو بودند که میتوانستند او را به یکی از آرزوهایش برسانند.
زاهدی پساز بررسی و اطمینان از مرغوبیت سنگ، از آن مرد خواست محل استخراج آن را به او نشان بدهد. مرد غریبه پذیرفت و این دو همراه یکدیگر از مجاورت حرم مطهر، ۲۵ کیلومتر را بهسمت شمال شهر مشهد پیمودند و در محلی بین دو روستای فارمد و جُغری توقف کردند. زاهدی مکانی در نزدیکی اژدرکوه خود را در میان گنجی یافت که میتوانست با آن شهری نو را بنا کند.
او بلافاصله دست به کار شد و برای احداث نخستین کارخانه سیمان در شرق کشور حتی از فروش خانه خود دریغ نکرد. زاهدی با کمک سرمایهگذارانی که جذب کرده بود، اقدام به خرید تجهیزات لازم کارخانه کرد.
همه کارها خوب پیش میرفت، اما فشار و استرس زیاد کار به حدی بود که او را از دیدن ثمره تلاشهایش محروم کرد. مؤسس کارخانه سیمان مشهد، سه سال پس از آغاز فرایند احداث کارخانهاش، در روز دوشنبه هشتم بهمن سال۱۳۳۵، بهدلیل سکته مغزی در شصتسالگی از دنیا رفت. یک سال بعداز درگذشت او اولین کیسه سیمان مشهد روانه بازار شد.
در طول هفتدهه این واحد صنعتی برخلاف بسیاری از واحدهای صنعتی تسلیم مسائل و مشکلات پیش رویش نشد و همواره رو به توسعه گام برداشت. کارخانه سیمان در سال۱۳۳۶ با ظرفیت تولید روزانه هفتادتن کارش را آغاز کرد.
این کارخانه در اولین دهه فعالیت و دقیقتر در مهرماه۱۳۴۶ با خرید اولین کوره دوار از شرکت کروپ آلمان توانست ظرفیت تولید خود را در خط موسوم به «قائم» به سیصدتن برساند. گام بعدی کارخانه در جهت توسعه در مرداد۱۳۵۴ با راهاندازی دومین کوره دوار ساخت شرکت پولی زیوس آلمان برداشته شد.
با راهاندازی تجهیزات جدید، ظرفیت تولید سیمان خاکستری کارخانه به ۱۲۵۰ تن در روز رسید. البته این خط با هدف تغییر تولیدات به سیمان سفید در سال۱۳۸۸ تعطیل شد تا با دمونتاژ ماشینآلات و تجهیزات، کارخانه سیمان مشهد به بزرگترین کارخانه تولیدکننده سیمان سفید کشور تبدیل شود.
این مجموعه که مرغوبترین سیمان سفید را در کشور تولید میکند، ارزآوری قابلتوجه دارد. سال۱۳۷۷ با خرید سومین کوره دوار با ظرفیت تولید روزانه ۳ هزار تن سیمان از شرکت افسیبی فرانسه، تحولی بزرگ در این واحد صنعتی ایجاد شد؛ پیشرفتی که مدیران و کارکنان کارخانه به آن هم راضی نشدند و پساز خرید کوره دوار دیگری با ظرفیت تولید ۳ هزار و ۴۰۰ تن کلینکر از شرکت افال اسمیت دانمارک، خط چهارم کارخانه را در سال ۱۳۸۹ وارد مدار کردند.
محیط هفتصدهکتاری کارخانه سیمان شباهت زیادی به یک شهر مردانه کوچک دارد. خیلیها اگرچه بنیانگذار این واحد صنعتی را ندیدند، اما قدردان او و همه کسانی هستند که پیش از آنها برای احداث و توسعه این واحد صنعتی زحمت کشیدند. هشتاددرصد از کارکنان کارخانه بومی روستاهای مجاورند. سیدمحمد فرجی پنجاهوششساله، از قدیمیترین کارگران کارخانه است و ساکن روستای جغری در مجاورت آن.
چیزی به دوران بازنشستگی سیدمحمد نمانده است. او خاطرات بسیاری از کارخانه دارد. میگوید: دوران کودکی من شغل ساکنان روستا کشاورزی بود. متأسفانه از اواخر دهه۶۰ و اوایل دهه۷۰، خشکسالیهای پیاپی و ورود فاضلاب شهری به داخل روستا، منجر به نابودی همه مزارع و درختان انگور شد. بعداز خشکشدن زمینها، برای مردان روستا، شغلی بهجز کار در کارخانه نبود و بسیاری از مردان روستا در اینجا مشغول کار شدند.
علی ادیبی یکی از فعالان این مجموعه است. او پانزدهسال گامبهگام سطوح مختلف را طی کرده است و حالا بهعنوان رئیس مکانیکی دپارتمان آسیاب مواد کارخانه سیمان خدمت میکند. ادیبی تعریف میکند: بعد از استخدام کارم را در پروژه راهاندازی واحد ۴ آغاز کردم. فعالیتم را ادامه دادم تا اینکه از سال۱۳۹۷ به خط تولید منتقل شدم.
با گذشتن از خط۳ و ۴ کارخانه به چشم بینای مجموعه یا همان اتاق کنترل میرویم؛ محلی که در شبانهروز، متخصصان بخش فنی مشغول بررسی عملکرد تجهیزات کارخانه در طول مسیر تولید هستند. اهمیت کار آنها به حدی است که یک لحظه غفلت، خسارت سنگینی به مجموعه وارد میکند و نباید لحظهای از اعداد و ارقامی که روی مانیتورها به نمایش گذاشته میشود، چشم بردارند.
ابراهیم زحمتکش، مسئول بهرهبرداری خط چهار کارخانه سیمان، مدیریت اتاق کنترل را هم برعهده دارد. او میگوید: در اتاق کنترل فرایندها و پارامترهای جاری را در مراحل تولید سیمان به دقت زیر نظر داریم. کار ما با مواد مذاب و حرارت است و نباید لحظهای از بررسی عملکرد سیستم غافل شویم.
حتی با دوربین ویژهای که در کوره نصب شده است، وضعیت مواد مذاب را کنترل میکنیم. دمای این محل تا ۱۶۰۰ درجه سانتیگراد هم میرسد. او ادامه میدهد: در این سیستم، بیشترین اختلالات را در اتاق پیشگرمکن شاهد هستیم.
محمدهادی درخشان ادامه میدهد: کارخانه سیمان مشهد اطمینان و اعتماد مشتریان را آسان به دست نیاورده است و بههمیندلیل همواره برای حفظ آن تلاش میکند. مطالعات و آزمایشهای زیادی روی محصولات حتی پیشاز استخراج سنگها از معادن انجام میدهیم. نمونهبرداری میکنیم و نمونهها را ابتدا در سنگشکن تا مرحله کوره و در نهایت آسیابهای سیمان آزمایش میکنیم.
مطابق با استانداردهای روز در آزمایشگاه تخصصی کارخانه که مجهز به تجهیزات روز دنیاست، مواداولیه و محصول نهایی را هم محک میزنیم و آزمایش میکنیم. اگر کیفیت خوبی داشت برای تولید اقدام میکنیم. البته ما به این جایگاه راضی نیستیم و همواره در جهت پیشرفت گام برمیداریم. سال گذشته در کارخانه سیمان سفید توانستیم با نیروی متخصص خود سیمان رنگی تولید کنیم؛ سیمانی که نمونه آن عید نوروز امسال در میدان فلسطین به کار گرفته شد.
درخشان میگوید: هرسال اعتبار شایانتوجهی را برای مسائل زیستمحیطی و ارتقای کیفیت فیلترهای کارخانه هزینه میکنیم تا میزان آلایندگی ما به حداقل برسد. سال گذشته، بیش از ۱۰ میلیاردتومان برای بهینهسازی فیلتراسیون خرج کردیم.
این موضوع را هم لازم است بگویم که ما دو نوع فیلتر بک و فیلتربرقی داریم؛ به ایندلیل که غبار برای ما سرمایه است و هرچه بیشتر جلو آن را بگیریم و به چرخه تولید بازگردانیم، هم به نفع ما و هم محیط زیست است. علاوهبراین تلاش میکنیم به صنعت سبز دست یابیم.
برای رسیدن به صنعت سبز، الزاماتی را باید در طول سال رعایت کنیم که توسط سازمان محیط زیست تعریف شده است. از سال گذشته این کار را آغاز کردیم؛ همچنین بهطور مداوم در هر سال هزارتا ۲ هزار اصله درخت سازگار با اقلیم شهر مشهد به فضای سبز مجموعه اضافه میکنیم، بهطوریکه امروز حدود ۳۵ هکتار از فضای مجموعه درختکاری شده است.
درخشان توضیح میدهد: یکی از مواردی که کار را برای ما دشوار کرده، قرارگرفتن نام کارخانه در لیست تحریم و اعمال تحریمهای ظالمانه علیه کشور است. این موضوع باعث شده است در تأمین بخشی از تجهیزات یدکی و برقی که ناگزیر هستیم از خارج کشور تهیه کنیم، با مشکلاتی روبهرو شویم. علاوهبراین در سالهای اخیر در مصرف برق و گاز هم محدودیت داشتهایم.
سال گذشته ما ۱۵۰ روز محدودیت مصرف داشتیم، آن هم در بازههای زمانی همچون خرداد تا شهریور که همواره در این بازه زمانی در کشور شاهد افزایش ساختوساز واحدهای مسکونی و تقاضای سیمان هستیم. متأسفانه محدودیتها باعث کاهش تولید و افزایش قیمت سیمان در بازار میشود.
میزان تولید ما به ۳ تا ۳ هزار و ۵۰۰ تن رسیده است. کارخانه سیمان با توجهبه شرایطی که دارد، باید دائم کار کند. کاهش تولید همچنین برای ما خسارتهای بسیاری دارد که مهمترین آنها فرسایش، استهلاک و خرابی تجهیزات کارخانه است. مسئولان باید توجه کنند دما در کورههای ما بین ۱۲۰۰ تا ۱۶۰۰ درجه است و یک لحظه قطع برق یا گاز، شوک بدی به خطوط تولیدی ما وارد میکند و خسارت چندمیلیاردی به همراه دارد.
امروز ۱۰۲۰نفر در این واحد صنعتی بهصورت مستقیم فعالیت دارند و بیشاز ۳ هزارنفر هم غیرمستقیم ازطریق کارخانه سیمان نان میخورند؛ کارکنانی که بخش آموزش برای بهروزرسانی دانش و مهارتشان برنامههای مداوم و کارگاههای آموزشی برگزار میکند.
میثم کیوانی، مدیر بخش آموزش کارخانه سیمان و مسئول روابط عمومی آن، میگوید: اولویت اصلی کارخانه سیمان در استخدام نیرو، روستاها و محلات مجاور بوده است. سال گذشته از بین صدودهنفر استخدامی بیش از نوددرصد آنها ساکن محلات و روستاهای اطراف ما بودند.
در همین راستا نیز کارگاههای آموزشی برای آنها و دیگر کارکنان برگزار میکنیم تا همواره دانش و مهارتشان بهروز باشد. همچنین کتابخانه مجهزی داریم که بیشتر کتابهای آن در حوزه این صنعت است.
او ادامه میدهد: علاوهبر این، درصدی از فروش محصولات را به انجام کارهای عامالمنفعه اختصاص میدهیم؛ از اهدای سیمان به مراکز آموزشی و مذهبی گرفته تا مشارکت در بهسازی و نوسازی مراکز درمانی چند روستا که هفته گذشته آخرین مورد آن به بهرهبرداری رسید.
این مجموعه در طول چند دهه اخیر، رقبای متعددی پیدا کرده است، اما همچنان محصولاتش بهعنوان یک برند در کشور شناخته میشود. محمدهادی درخشان، مدیر فنی کارخانه سیمان، درباره حجم تولید این مجموعه میگوید: در این واحد صنعتی، دو خط تولید سیمان خاکستری داریم که روزانه ظرفیت تولید ۳ هزارو ۴۰۰تن را دارند.
خط تولید سیمان سفید نیز که در سال۱۳۹۳ به بهرهبرداری رسید، روزانه هزار تن تولید دارد و بزرگترین تولیدکننده سیمان سفید کشور شناخته میشود و با اطمینان میگویم که میزان سفیدی و مرغوبیت آن در ایران نمونه است. این ویژگی باعث شده است ما مشتریان بسیاری از ۲۴ کشور جهان داشته باشیم.
وارد روند پیچیده خط تولید میشویم. مواد خام استخراجشده از کوه وارد سنگشکن میشوند. سنگهای بزرگ پس از تبدیلشدن به تکههای سنگ کوچک و ریز به بستر اختلاط منتقل و آنجا ذخیرهسازی میشوند. در گام بعد، این سنگها وارد آسیاب مواد میشوند و آنجا به اندازههای ریز تقلیل سایز پیدا میکنند. پساز ریزشدن، سنگها به سیلوی همگنسازی مواد وارد میشوند تا در آنجا بهصورت یکنواخت درآیند.
برای وارد شدن به داغترین بخش خط تولید یعنی کوره دوار ذخیره میشوند. سنگهای ریز که با مواد دیگری ترکیب میشوند، بهترتیب وارد بخش پیشگرمکن میشوند. این مواد در بخش نخست، دما تا میزان نهصددرجه سانتیگراد را تجربه میکنند. سنگها پساز بالا و پایینشدن در بخش پیشگرم، وارد بخش کوره که دمای آن حتی به ۱۶۰۰درجه سانتیگراد میرسد، میشوند.
این دما همهچیز را تبدیل به مواد مذاب میکند. این مواد مذاب که درواقع کلینکر هستند، در پایان برای سردشدن با دمای محیط به بخش آخر منتقل میشوند. (کلینکر محصول نهایی کوره سیمان است). کلینکر در گام بعد با حدود ۴ درصد سنگ گچ در آسیاب مخلوط و تبدیل به سیمان میشود تا بتوان آن را در سیلو ذخیرهسازی کرد؛ در پایان با انتقال به قسمت خروجی سیلو، برای بستهبندی تحویل بارگیرخانه میشود.